Production of Metal Parts
During the recent years our production is even more involved with the manufacturing of metal parts.
This includes a broad range of parts, for example: turn parts, milling parts, parts obtained through CPU machines processing; parts with complex geometry; fine parts with grinding of surfaces; threading elements; spare components; parts associated with electroerosion processing; welded components; parts with high quality of surfaces and polished parts.
We work with many types of material – hard or soft metals, ferrous or non- ferrous metals, different types stainless steel; dense or porous materials; these can be processed with high precision.
The processing methods associated with details are strictly optimized and human interferences, if possible, are minimized. Therefore, we have minimum bending and deformation risks. In view of the production process we adhere to all technological requirements and standards, so that we achieved the desired results – high quality of the products.
We produce single details with simple and complex geometry but we have also serial production of details with small, medium and large volumes. We have capacity to produce a broad range of parts as follows:
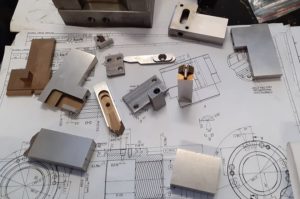
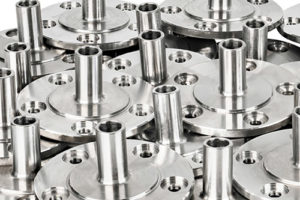
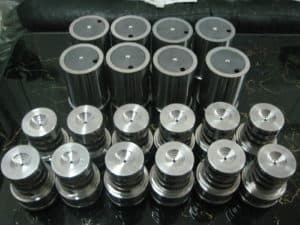
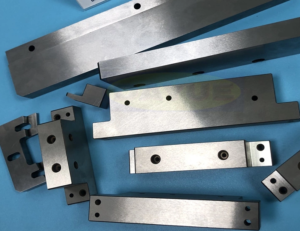
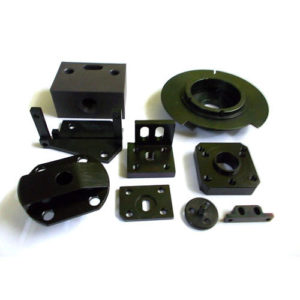
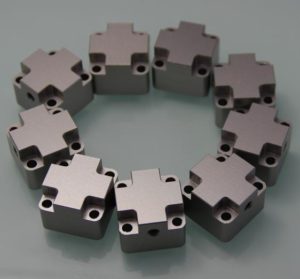
We offer the potential to produce a broad range of parts as follows:
- turning parts
- milling parts
- base details
- details produced by electroerosion
- parts with complex geometry
- precise parts
- serial production details
- spare parts
- details produced through CPU machining
- details with laser cutting process
- welded components
- non-metal details (plastic, wood and other materials)
- details with grinding operations
- threading elements
- hardened elements
- stainless steel details
- polished details
- galvanized details
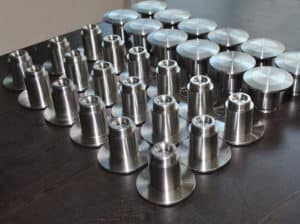
Lathe Details
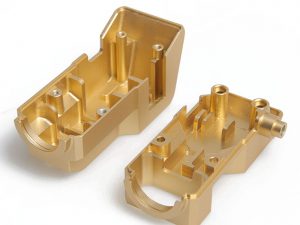
Parts with Complex Geometry
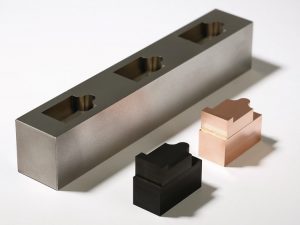
Details Produced Through the Power-erosion Method
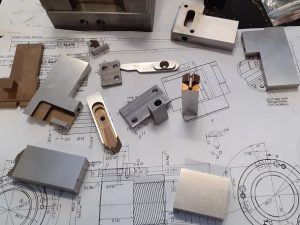
Fine Details
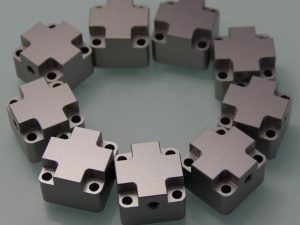
Cutter Details
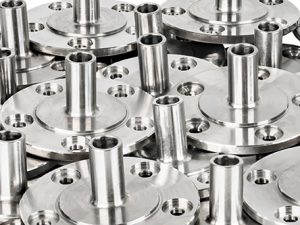
Stainless Steel Details
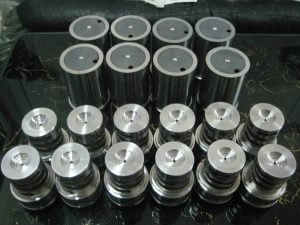
Serial Production Details
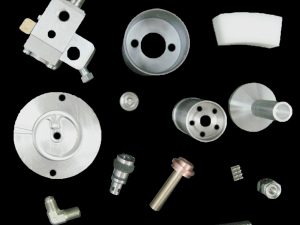
Spare Parts
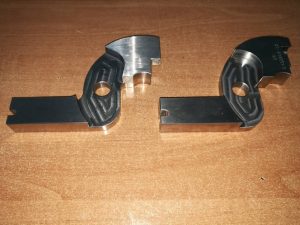
Details Produced Through CPU Machines
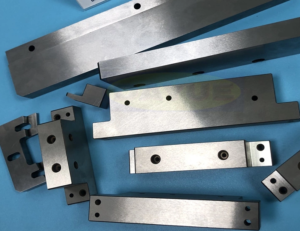
Polished Details
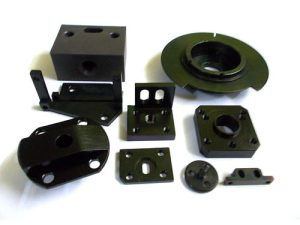
Oxidized Details
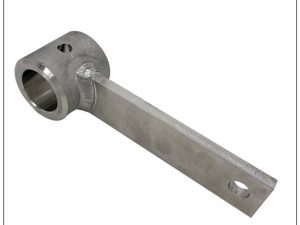
Welding Components
In our machine workshop can be performed the following operations:
- Project tools and design of drawings
- CNC milling
- CNC turning
- Conventional lathe turning operations
- Conventional milling operations
- Drilling, Boring, tapping, threading
- Flat surface grinding
- Cylindrical surface grinding
- Profile grinding
- Welding
- Wire-cutting erosion processing
- Spark erosion processing
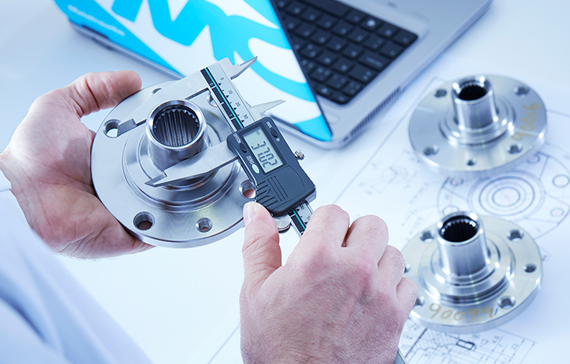
We strictly adhere to all technical requirements associated with the produced elements. During and after the production process we monitor and control the basic parameters of the produced items – geometry and precision of the sizes, as well physical characteristics.
In order to provide high quality we rely on regular inspection of elements after each operation and detailed inspection after all production process in relation to achieve all requirements associated with the specific detail.
In addition to the standard measurement methods, we also use modern techniques such as 3-coordinate sensor measurement and visual measurement through an optical machine
In order to improve the physical and mechanical properties we use a wide range of heat treatment processes for materials:
Normalization, annealing, volume hardening, surface hardening, nitriding, carburizing, plasma nitriding, etc. In relation to this we use also chemical and electro-chemical coating processes. These can be introduced for the metal parts, namely: oxidation, zinc coating, nickel coating, chrome coating, electro-chemical polishing, anodizing, use of titan and phosphates, etc.
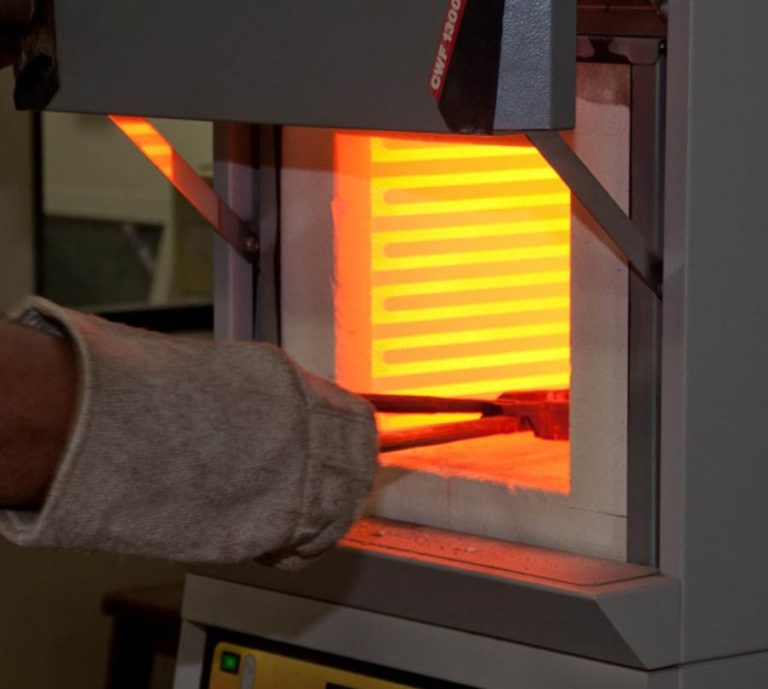
Special attention should be directed toward the observation of terms regarding the received orders. The comfort and reliability for our clients from this perspective are very important, so that we guaranteed a long-term and trustworthy partnership.
The perfectionism related to the packaging of the produced metal parts will bring confidence regarding the parts we produce. We carefully order and package all details and we make no exceptions. This refers to big and small packages and large products arranged on pallets.
We work with several shipping companies who provide reliable transportation at good prices to all parts of Europe.
More About Our Services
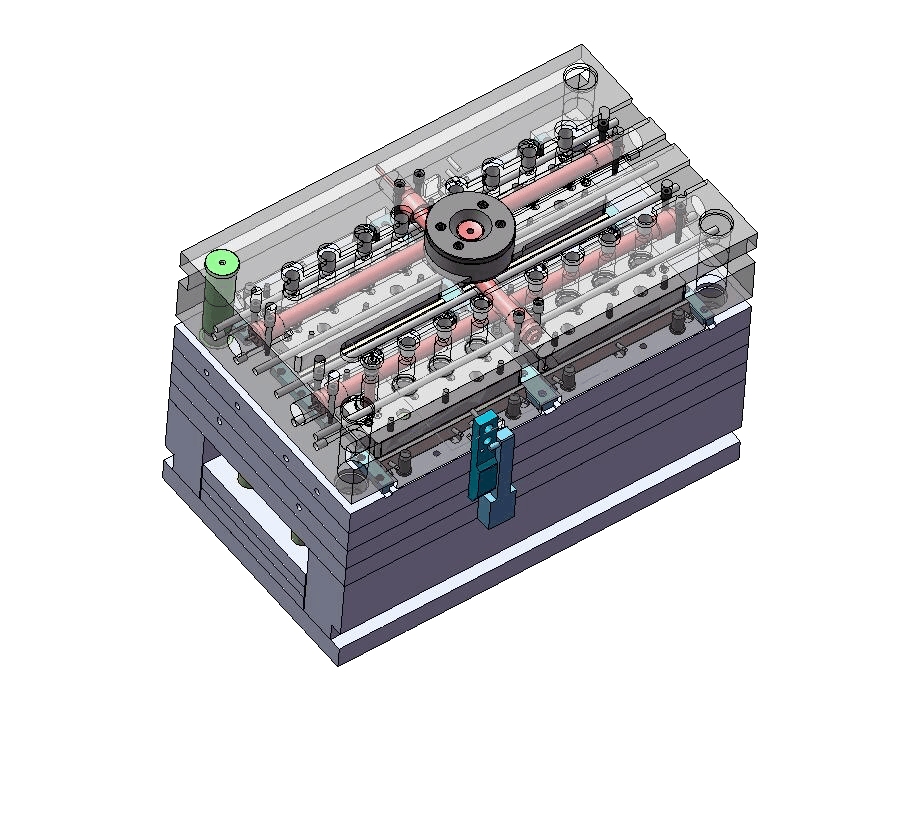